Från artikeln nedan lär du dig hur gör det själv gör en kolvmotor av trä. Följande beskrivning och instruktioner är hämtade från Matthias Wandel YouTube-kanal.
En av kompisens vänner är en modellerare - designer. Han skapar olika modeller av fartyg, bilar och olika kraftverk. Det var han som bad sin vän att göra modellen En trämotorkolv som går på tryckluft.
Här är ett exempel på ritning och detaljer om denna motor.
För att tillverka denna motor krävdes följande material och verktyg:
- en liten bit plywood 10 mm.;
- träblock;
- bandsåg;
- en mejsel;
- klämmor;
- borrmaskin;
- borr 4 mm;
- Forstner borr;
- mallet;
- PVA-timmerlim;
- lack;
- en hyvel;
- en penna;
- släpp;
- 38 mm skruvar;
- skärkniv;
Produktion av cylinderdelar från plywood.
Fasad montering av cylinderdelar.
Utsikten bakifrån.
En av de svåraste delarna att producera i en motor är vevaxeln. Motorns vevmekanism är faktiskt belägen i närheten av svänghjulet, men en ytterligare mekanism behövs för att aktivera ventilenheten. Denna sekundära enhet består av en 6 mm bar. Befälhavaren gjorde det genom att lima en bit av stiftet på huvudaxeln. Den andra delen av stiftet skärs i form av en halvmåne i tvärsnitt, vilket gör att den kan passa tätt mot axeln. Därefter skars en del av huvudaxeln till önskad längd.
Den första skärningen gjordes med en bandsåg, och resten klipptes försiktigt för hand.
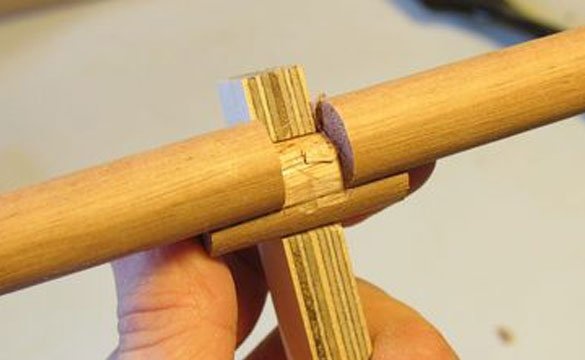
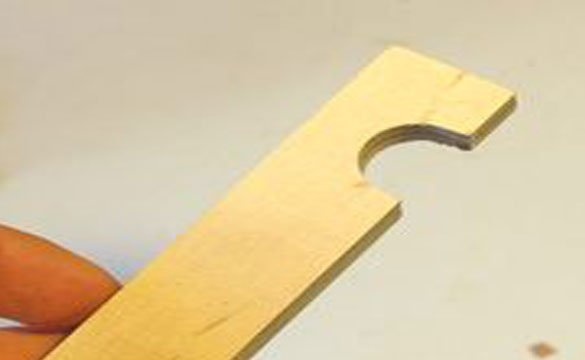
Styrningen är tillverkad av plywood, i vilken ett hål borras från kanten. Sedan skärs hålet i hälften. Således gjordes en mall för att ta reda på hur mycket mer material som måste klippas så att delarna spolar.
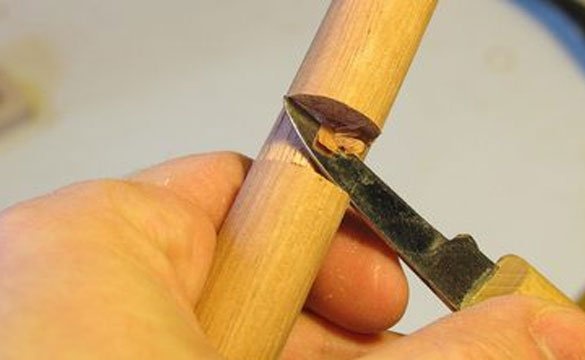
Genom att trycka guiden ordentligt mot den klippta sektionen och vrida den fram och tillbaka såg befälhavaren axelsektionerna från vilka det var nödvändigt att ta bort materialet.

Så fort befälhavaren var övertygad om att den mellersta delen av vevaxeln var ganska rund, gjorde han två förstärkningsplattor, som han skulle hålla fast på vardera sidan av den. Han borrade två 15 mm hål i plywood med ett mittavstånd på 6 mm. Därefter klipptes en rektangel runt dessa hål.Som ett resultat limmades de erhållna delarna på vevet. Limning av dessa bitar var en enkel fråga - du var tvungen att trycka dem från ändarna på vevaxeln.

Klar vevaxel (efter lackering)
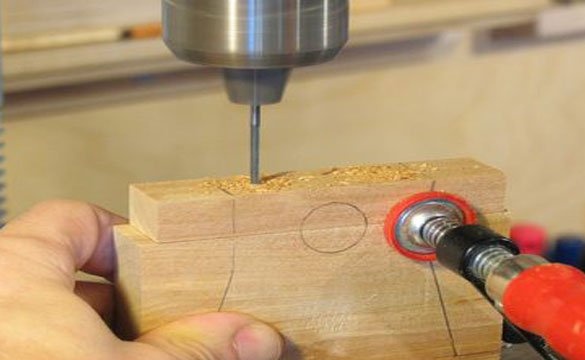
Vevaxelens lagerblock består av två delar. För att säkerställa att alla hål var perfekt inriktade, klämde befälhavaren ihop båda halvorna av lagret och borrade sedan hål för skruvarna genom dem.
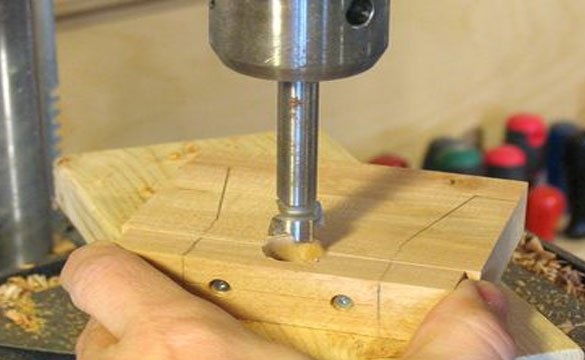
Efter att ha skruvat den övre delen av lagerblocket, borrade befälhavaren ett hål för axeln genom båda delarna. Han använde en 15 mm borr. Efter att ha borrat hål skärde befälhavaren ut hela blocket med lager med en bandsåg och rundade hörn på den.
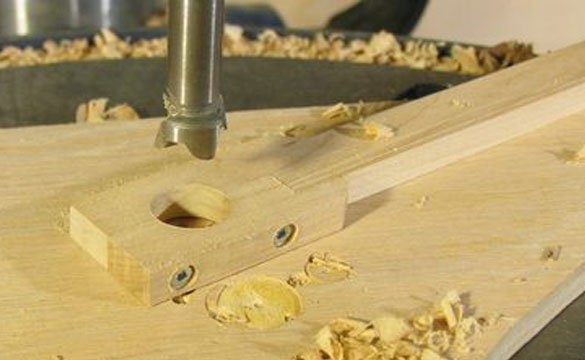
Befälhavaren använde samma tillvägagångssätt för att skära hål i anslutningsstången. Först vred han delarna ihop och borrade sedan ett hål i den monterade stången.
Vevaxel med anslutningsstav.
Svänghjul med vevaxel. Svänghjulet är skuren ur plywood. Den har hål för balansering.
För att ansluta svänghjulet till vevaxeln används en liten limmad plywood, till vilken vevaxeln är fäst med en skruv.
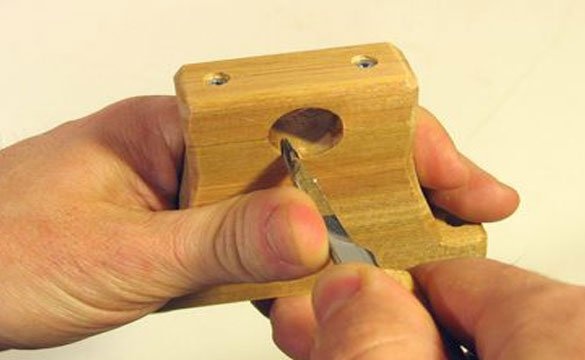
I slutändan justerade befälhavaren något i lagren och skär ett mycket tunt skikt av trä från insidan med en skärkniv. Denna procedur måste upprepas igen efter att allt målats, eftersom lacken tillförde lite tjocklek.
Montering av vevaxeln i lager på plywood - stativ med självgängande skruvar.
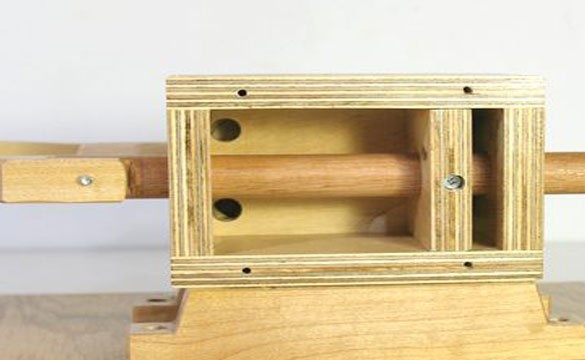
Cylindern och kolven är gjorda rektangulära.
Det finns inga kolvringar eller tätningar runt kolven, så det finns "rensningshål". Denna motor är inte konstruerad för hög effekt och effektivitet, så allt är i ordning. Helst bör det finnas en liten frigång runt kolven för att minska friktionen, ungefär 0,1 mm. Befälhavaren gjorde en kolv så att han inte hade ett mellanrum och polerade den sedan lite.
Det finns inga packningar i denna enhet. Detaljer är helt enkelt skruvas ihop. Detta räcker för att minska gasläckan till en acceptabel nivå - det finns naturligtvis mycket mindre läckor runt locket än runt kolven.
Bilden visar hål på baksidan av cylindern för luftinlopp. Luftinloppen för kolven bör riktas mot kolvens ändar, men ventilaggregatet måste vara inlopp ihop så att en inre kanal bildas mellan plywoodens två delar genom att skära ut plywoodskikten. Befälhavaren gjorde dessa håligheter med en Forstner-borr. De är inte synliga när motorn är monterad, så det är inte kritiskt.
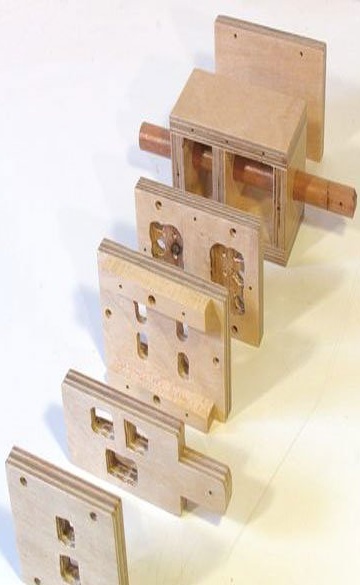
Dessa bilder visar alla detaljer om kolvblocket och ventilen. De två hålen på framsidan av plywood är luftinloppet och utloppsöppningarna. Genom att byta inloppsröret, som blåser (eller suger), kommer motorn att arbeta i motsatt riktning.
Alla delar av ventilenheten är lackerade. För att få produkten att se jämnt uppsvälld polerade mästaren mellan lagren. Det tog lite slipning för att få ventilerna att glida lätt.
Hela enheten är fäst med 19 mm träskruvar med en diameter på 4 mm. Totalt 38 skruvar.
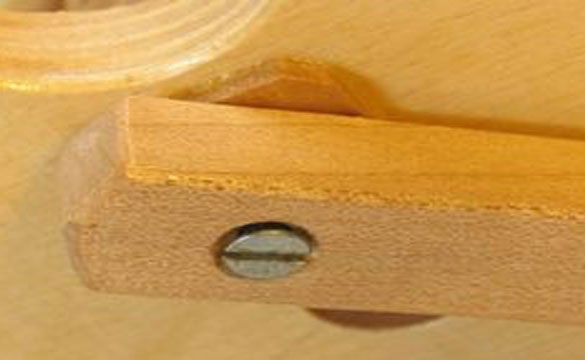
För montering av lagret på anslutningsstången användes en avskuren självuttagande skruv 38 mm lång. Befälhavaren var tvungen att klippa bort änden på den självspännande skruven så att han inte sticker ut på andra sidan av svänghjulet för långt. Det fanns helt enkelt ingen annan hårdvara tillgänglig.
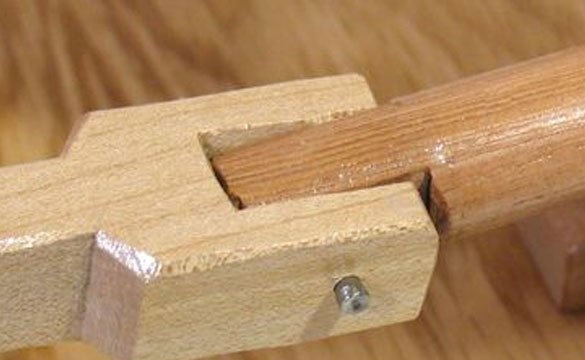
Kolvänden på anslutningsstången är ansluten till kolvstången med en enkel stålstift, som är gjord av en knubbig spik. Hålet i kolvstången borras lite mindre så att fingret sitter tätt mot kolvstången. Anslutningsstavens hål är något förstorade, vilket gör att kopplingsstången kan rotera fritt på stiftet.
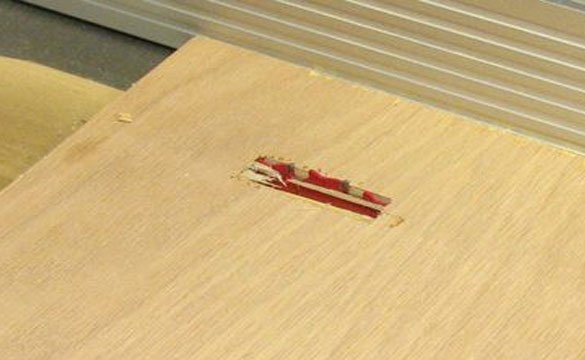
Hela motorn är monterad på en bit plywood.
För denna motor skapade befälhavaren ett svänghjul, så stort som möjligt. Därför var jag tvungen att klippa ett spår i monteringsplattan så att den sticker inåt.
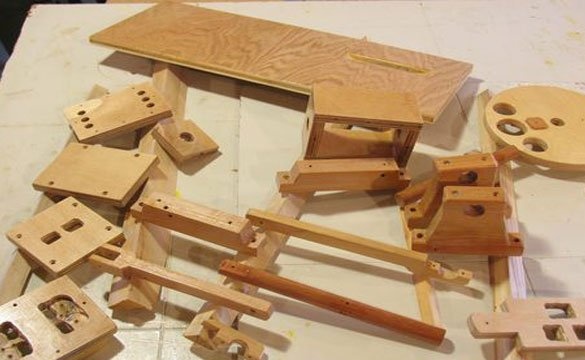
Befälhavaren byggde hela motorn och såg till att den fungerade smidigt, först då målade han alla detaljer. Bilden visar torkning av delar.
Motorns lackering krävde förfining för att motorn ska fungera normalt igen.
Men själva lacken var inte tillräckligt halt, och i slutändan, så att vevaxeln inte skulle knäcka, oljades den.
Kontrollera motorns prestanda.
Om du vill hemgjorda produkt författare, försök sedan upprepa och göra. Tack för din uppmärksamhet. Vi ses snart!