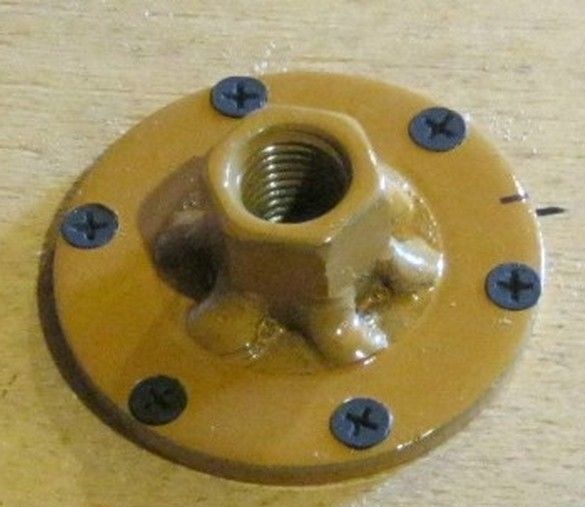
Har konstruerat trä svarv, hade lite kul med enkel vändning i centren. Efter ett tag blev det nödvändigt att bearbeta mer olika arbetsstycken. Jag var tvungen att flytta hjärnan, som från improviserade medel, utan tillgång till en tredje part svarv (för metall), göra lämplig utrustning. En av mönster visade sig vara mycket billig, bekväm och efterfrågad.
Snap-in-fixturen bestod ofta av två delar - en universell liten metallplatta och en specialiserad trädel. En metallplåt kan också användas som vanligt genom att fästa skruvar på arbetsstycket.
Vad användes.
Verktyg.
Själva trä svarven, skärare för det, en uppsättning bänkverktyg. Du kan inte göra utan en skärmaskin (slipmaskin), det är bättre att använda en liten - det är mer bekvämt och säkrare. Hörlurar för både fotografering och skyddsglasögon eller visir. Ta heller inte ut utan svetsning - en liten växelriktare och tillbehör. Elektroder 2,5 mm. Ofta används smältning. Det är nödvändigt att varken borrning, mer bekväm och mer exakt, det är klart, maskinen.
Material.
Egentligen är det bara rätt antal muttrar och brickor. Det är bättre att måla det färdiga metallstycket och sedan måla. Ett litet träd för "smal specialisering", jag använder ofta torrt björkved med jämna lager.
So. Spindeln på min svarv slutar med en M16-tråd som gör det möjligt att använda standard hårdvara. I detta fall är detta en "förlängningsmutter." Den skärs i hälften direkt på maskinen, slås på och roterar. Vinkelslipare. Det ska skäras försiktigt. Först på en avstängd maskin och med en tomkvarn i händerna, försök försiktigt på, så att det är bekvämt, var än armbågarna är och för att inte passa in i något som roterar.
Maskinen slås på och efter att ha antagit en förprovad ställning som ingår i kvarnen slår vi märket på markören mitt i den roterande muttern. Speciellt försiktigt först, tills kanterna sågas, då börjar den skära jämnare och trycket kan höjas något.
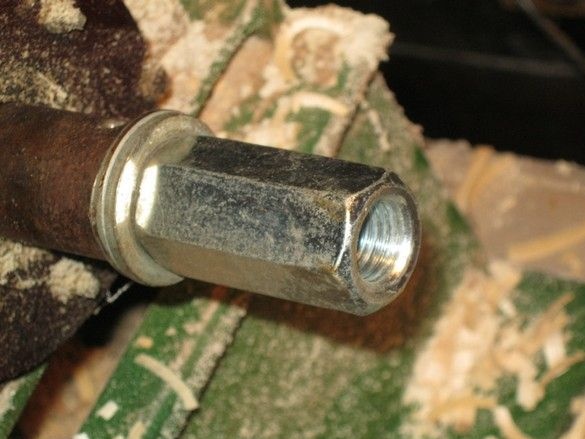
Efter en tid av våra ansträngningar skärs mutterns vägg igen och halvan faller bort.Höjden på varje hälft, med hänsyn till snittets bredd, visar sig vara något större än sin vanliga syster som inte är "förlängning". Längden på tråden på min maskins spindel tillåter inte användning av en vanlig mutter - den sticker ut under den färdiga frontplattan och orsakar mycket besvär senare, när du arbetar.
Nästa steg är svetsning. Från standardutbudet av hårdvara tar jag en "förstärkt bricka", i vissa butiker kallas det en "karossbricka" med lämplig diameter. Vanligtvis är detta nästan det största av det tillgängliga sortimentet. Du måste kontrollera om muttern faller i den. Mutteren ska stå i mitten av hålet i brickan. En skuren mutter kommer att stå bättre - det kommer inte att finnas någon avfasning på ena sidan av den, detta bör tas med i beräkningen när man försöker på en ny i butiken.
Den avskurna halvan svetsas till brickan. Prydligt. Det är väldigt bra att först dra åt dem med en klämma, men vanligtvis visar det sig ganska bra. Ribbbenen svetsas i följande ordning - vilket som helst, motsatt. Arbetsstycket roterar 90 grader, återigen någon av de två, sedan motsatt. Så det är mindre chans att muttern kommer att glida från brickan. I de första exemplarna försökte jag faktiskt organisera ett "spår" med samma kvarn på den roterande halvan av muttern, för en säker passform i hålet, men vinkelsliparen är inte det verktyg som kan göra det här jobbet bra - ofta på grund av den inte så jämna kanten på "spåret" , var muttern inte särskilt i linje med brickan.
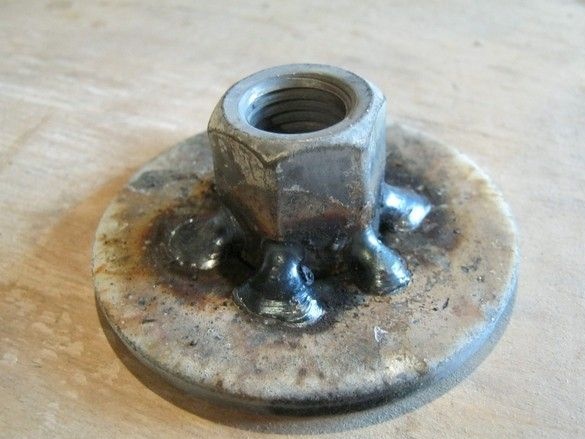
Efter kylning av arbetsstycket, som vanligt, omsluter vi glasskorpan med slagg och sätter arbetsstycket på maskinspindeln, under rotation utvärderar vi utloppet, om de är inom rimliga gränser, korrigerar vi den medföljande vinkelsliparen.

Det är möjligt för estetik och på baksidan. Här, skärpa med en penna på rätt plats för det roterande arbetsstycket, noterar vi diametern längs hålen kommer att borras. För att använda den framtida frontplattan med relativt stora föremål, kan de borras mer, upp till sex, om det gäller bagateller - tre, fyra.
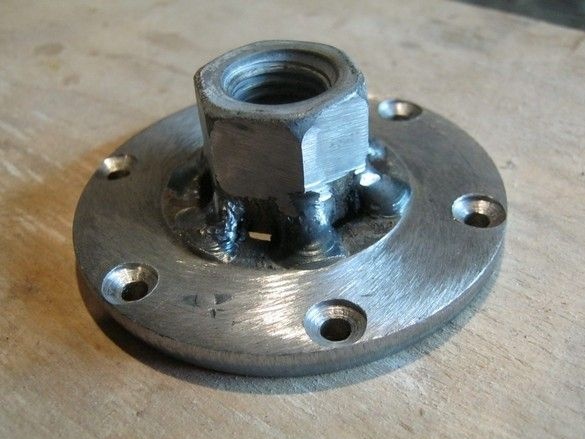
Efter det skulle det vara trevligt att måla tills det är rost - zinkskiktet är delvis bränt, delvis tömt. Nedan poppade "ockra" från en sprayburk, i två lager, även om jag vanligtvis är lat.
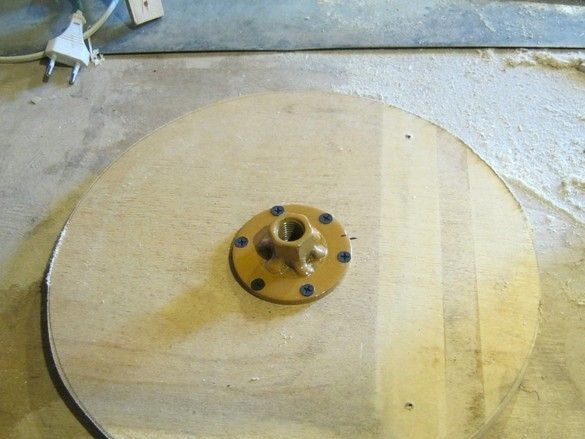
På bilden är den färdiga frontplattan på slipskivan gjord av tjock plywood. På en skiva undertryckt limmas PVA-lim, medelstora, ett sandpapper på trasbasis. Genom ett lager tidningar så att du kan riva av den slickade svetten.
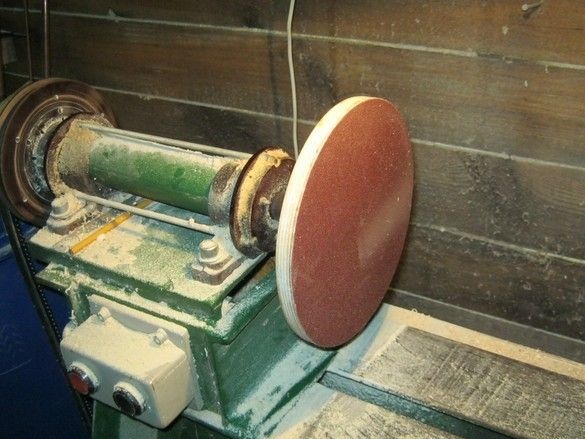
För att slipa verktyget, montera små träbitar innan du limar.
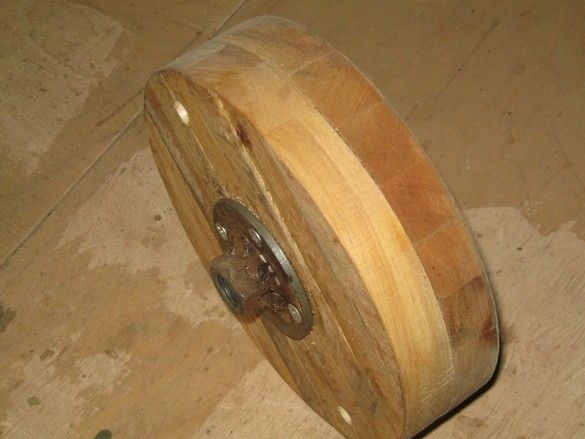
En liknande kontrast, men mindre i diameter och limmad från björkblock i två lager med överlappning. För skärpning av vridverktyg. I slutet finns det samma sandpapper, ett läderbälte limmas längs omkretsen för finjustering med GOI-pasta.
Och slutligen användningen av vår frontplatta för aktuellt arbete. Som den vanliga är vår lilla en praktisk att använda där du behöver montera arbetsstycket i ena kanten, utan bakre mitt. Samtidigt är det mycket bekvämt att lima arbetsstycket på mellanblocket. En bit av kortet är inte fäst med långa skruvar och vänds till en bekväm diameter, arbetsstycket är redan limmat på det. Smältlim.
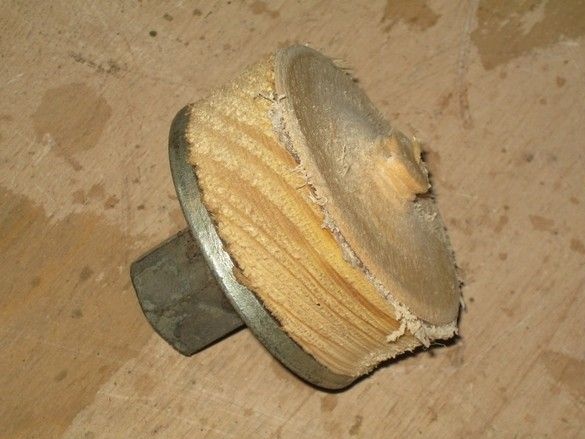
På fotot finns en sådan "patron", med en gröda kvar från arbetsstycket. Innan den nästa klistras in läggs frontplattan i maskinen och "skärs av" med ett skärverktyg, och skär av resterna av den limmade. Samtidigt är det nödvändigt att fånga en del av det gamla limskiktet så att det (limet) inte samlas för mycket.
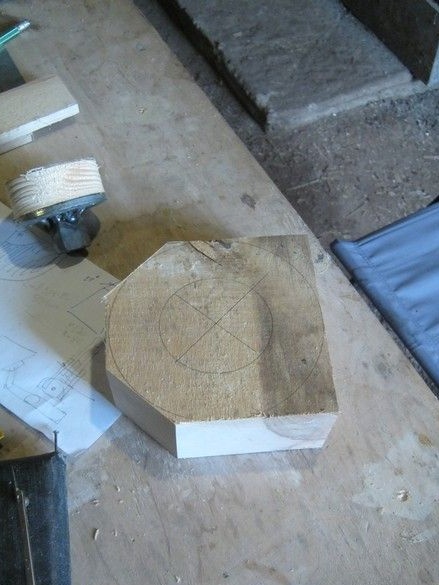
Arbetsstycket är markerat, medan bland annat en kompass, en cirkel med diameter dras något större än "blocket" på frontplattan. Detta gör att du kan orientera den exakt när den är limmad.
Jag smörjer båda ytorna som ska limmas med hett lim, inte nödvändigtvis helt, omkretsen runt omkretsen är tillräckligt, centimeterna ryggar bort från kanten.
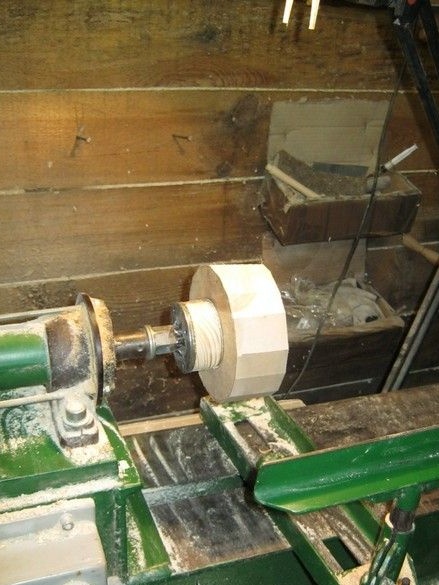
Inledningsvis är det bättre att trycka på arbetsstyckets bakre mittpunkt innan det är helt "lurar", då det inte finns några stötar, tas det bort.
Skönheten med en sådan installation är genom blocket, i de betydligt mer ekonomiska utgifterna för materialet i arbetsstycket, dessutom, när du vrider, behöver du inte ständigt komma ihåg hur länge skruvarna är för att inte klättra skäret till deras djup.
Tja, till dessert - det finns flera alternativ för ett mer specialiserat verktyg baserat på den tillverkade frontplattan.
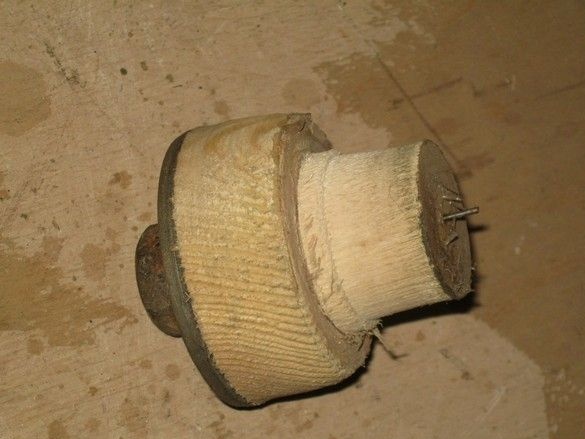
Till exempel den här krävdes att något vred mycket exakt kring det befintliga centrumet - lika enkelt som att beskära päron.
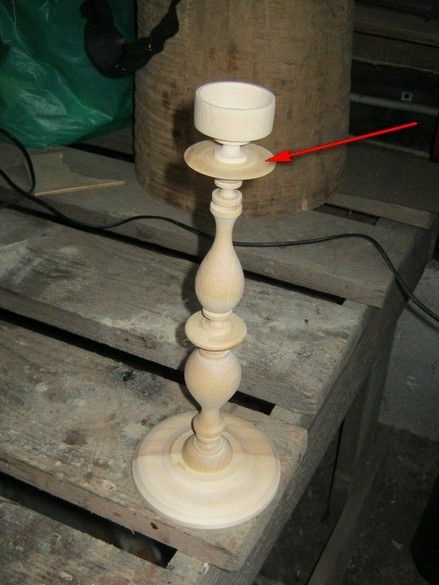
Eller till exempel - en del av en ljusstake gjord av 6mm plywood eller en tunn björkplatta. För dess fastspänning och bearbetning gjordes en sådan snäppning.
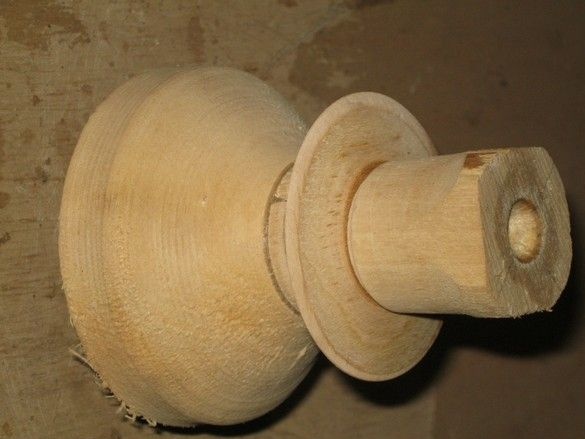
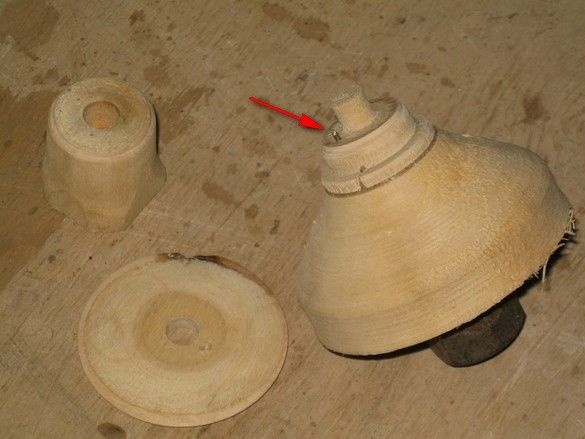
Skarpa kryddnejlika förhindrar att arbetsstycket vrids. Sammansatt, åtdragna av den bakre mitten.
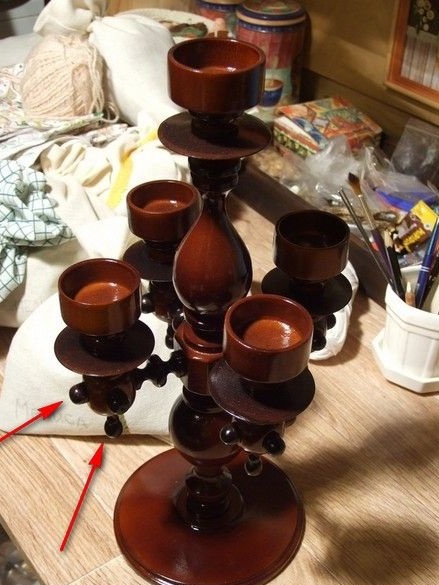
Vid tillverkningen av ljuskandelan krävdes ett antal små delar, till exempel navlar, jag var tvungen att skapa en enkel trächuck.
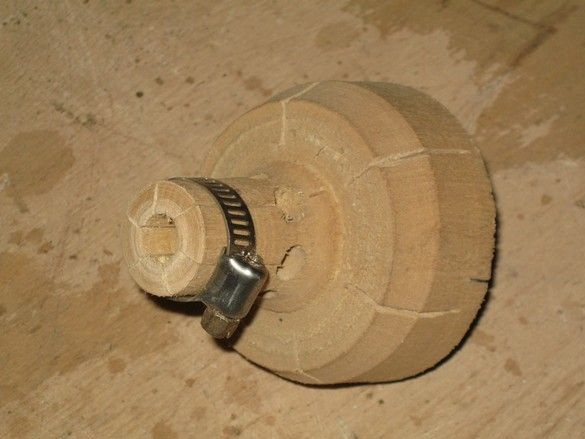
Trots de något begränsade kapaciteterna har det också ett antal fördelar, nämligen lättillverkning, låga kostnader. När man behandlar miniatyrdelar, nära de mest ”käftarna”, bör man inte vara för rädd för att haka ”patronen” med ett verktyg, som i fallet med en metallfabriksanalog ibland får dödliga konsekvenser. Ja, säkerheten är återigen ett minimum av utskjutande delar, de kan minskas ännu mer om du byter ut en metallmaskklämma med glödgat stål eller koppartråd eller till och med gör en liten avsmalning på utsidan av käftarna och fyller ringen för fastspänning. Metall eller trä.
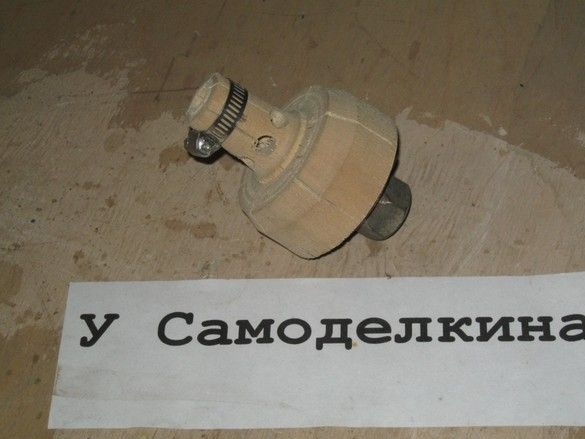
Vid tillverkningen av en spännchuck vrids först cylindern, ett centralt hål (en borrmaskin) borras, hål markeras och borras på sidan. Sedan bearbetas den framtida klämman i svarven - icke tjocka käftar bildas. Till sist skar han ned skär av kronbladarna.