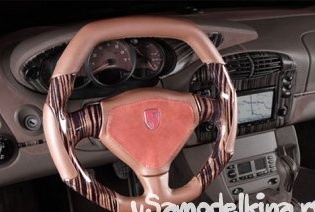
Det högra hjulet är aldrig runt. Och han är inte tunn. Och ännu mer utan trä- eller kolskydd och anatomiska kottar täckta med perforerat läder. Så många ägare av avstämda bilar tror. Och från mig själv lägger jag till att det är användbart för en bra ratt att ha en certifierad design med en airbag. Så, rätt hjul kan erhållas genom att ställa in fabriksratten.
Olika experter utövar olika metoder för tillverkning av skär och anatomi på rattet. Jag föreslår att man använder matristeknologi baserad på lermodellen. Fördelen med plasticin i effektiviteten av att söka efter modellens form. Fördelen med matrisen är möjligheten att återanvända vid tillverkning av samma roder eller fragment av skorpor för roder av andra storlekar.
Rattens mittdel behöver inte ingripas av en tuner, krockkudden ska fungera ordentligt. Endast kanten och delvis nålarna får uppgraderas.
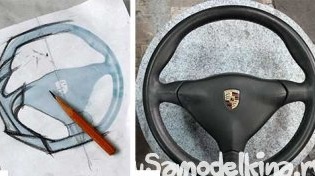
01. Utformningen av fälgen, du kan försöka helt enkelt kopiera från en befintlig ratt, men du kan drömma upp med själva formen. Det enklaste sättet att föreställa sig det eftertraktade rattet är att måla dina konturer på bilden av givarens roder. Men enligt min mening bör du inte dröja kvar på papper under lång tid, eftersom de ergonomiska kraven och utformningen av rattet kan förstöra dina ohämmade fantasier.
02. Det är särskilt trevligt att förbättra den dyra ratten i en prestigefylld bil, även om det är värt något enklare att pröva på din hand.
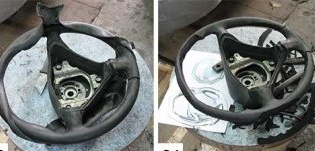
03. De flesta av rattarna i moderna bilar är täckta med läder, som jag skjuter först. Ett mjukt fälgskal öppnas under huden.
04. Om vi bestämde oss för att ändra rattens yttre kontur, måste vi avskärma överskottet av gummi från fälgramen. Men engagera dig inte i rengöring av ramen från gummi, det är bättre att lämna den på platser där den inte stör formförändringen.
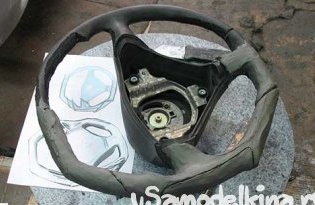
05. Och nu, på ett fritt sätt, försöker vi leta efter rätt proportioner och handvänliga formkonfigurationer på rattet gjord av plasticin. Jämför det ergonomiska handgjutet från plastin med det ursprungliga rodermönstret. Vi överför karaktäristiska bulor, bucklor och uttag från ritningen till plasticinen och "pumpar" igen rattets bekvämlighet längs armen.
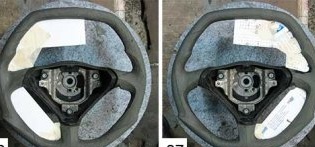
06. Vi börjar räkna ut den ungefär fastmonterade formen av rattet på ena sidan. Samtidigt är den eviga tvisten att det viktigaste är plasticine eller kitt jag löser till förmån för kitt.Det betyder att jag inte polerar plasticinen till en spegelfinish för att ta bort en nästan färdig matris, utan kommer att ändra oegentligheterna som finns kvar på plasticinen på det färdiga rattet med kitt. Men på plasticin måste vi markera linjerna med spår för att lappa huden, och sprickorna i plastformen med spetsiga revben. Ta bort mallarna från den tjocka kartongen från den färdiga plasticinen på hälften av rattet.
07. Vi överför konturer, linjer med sprickor och kanter på formen via mallen till leran på andra sidan av ratten. Bagelens sidotjocklek kan kontrolleras med en bromsok och jämför motsvarande platser till höger och vänster.
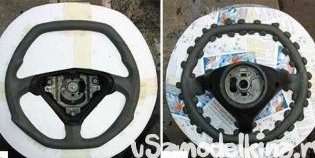
08. Och nu är formen byggd upp, men rusar inte med att kasta ut konturmallarna. Med deras hjälp måste vi göra en formning för att forma flänsarna på anslutningen på matrisens halvformer.
Liksom alla inneslutna volymer kan ett fast ratt erhållas genom att limma formens övre och undre skorpor. För att tillverka dessa glasfiberhalvor måste vi först göra en formform från en modelleringsmodell. En kontakt längs flänsarna delar rattmatrisen i två separata halvor, i vilka det är lätt att göra de övre och nedre skorporna på själva styrdelarna.
09. Flänsernas forskalning måste installeras strikt i planet för den bredaste längsgående delen av rattet. Jag fixar vanligtvis kartongforskalningsplattan med plasticinbitar på baksidan.
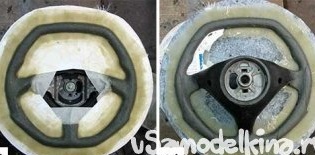
10. Arbeta med glasfiber, och särskilt kontaktgjutning av glasfiber impregnerat med polyesterharts, ger praktiskt taget obegränsade möjligheter för tillverkning av tredimensionella former. Material i flytande tillstånd omsluter ytor med vilken krökning och konfiguration som helst. En härdad komposit kan användas fullt ut för det avsedda syftet. När jag bildar grova matriser använder jag vanligtvis inte gelcoats (ett speciellt tjockt harts för arbetsytan) och dyra matrishartser. Men jag medger att jag ibland "missbrukar" tjockare-aerosil (glaspulver). Mitt relativt tjocka harts täpper modellens grovhet och fyller de skarpa hörnen på formen. Men formkvaliteten påverkas också av förstärkningsmaterialet. De första par skikten, särskilt på en komplex yta, Jag täcker den med 150 eller 300 glasfibermatta. Jag rekommenderar inte att applicera många lager på en gång - detta kommer oundvikligen att leda till deformationer i glasfiber. Efter en eller en halv timme blir hartset fast, men polymerisationsprocessen pågår fortfarande.
11. Under tiden kommer den första gjutningen att polymerisera, jag vrider rattet och tar bort kartongformningen. För att förhindra att hartset klibbar fast vid formen, belagde jag det tidigare med en vaxbaserad separationsförening (Teflon) bilar polish).
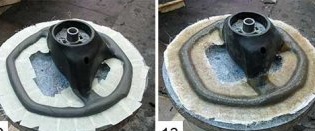
12. När det inte finns någon separator till hands och tiden inte tål, förseglar jag kontaktytan med maskeringstejp. Det är lätt att ta bort från härdad polyester. Så den här gången stängde jag flänsen.
13. Modellens undersida är också täckt med ett glasfiberlager. Efter att hartset har "stigit", det vill säga, först vände det från en vätska till en geléliknande, och sedan till ett fast tillstånd, vänder jag rattet igen. Jag applicerar ett skikt av tjockt glasmattor av klass 600 på framsidan av modellen, efter att ha rengjort det tidigare plastlagret med sandpapper. Så, växelvis applicera skikt, ökar jag tjockleken på matrisskal till 2-2,5 mm (vilket motsvarar 1 lager glasmatta märke 300 och 2 lager märke 600).
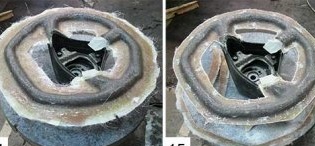
14. Den helt limmade matrisen upprätthålls under ungefär en dag, även om under bildning av konstant rusning på kvällen är den formade matrisen redan på morgonen på väg att arbeta.
15. Flexibel och mjuk i det flytande tillståndet glasfiber, härdning visar sin list. När jag tittar på dess lollipopyta, vill jag hålla den för hand. Men osynliga, utskjutande glasnålar kan allvarligt skada din hand. Därför rengör jag först och främst matrisytan med sandpapper. Den raka, stickiga kanten på matrisen måste klippas och lämna en fläns 25-30 mm bred. På ett avstånd av 10 mm från modellens kant är det nödvändigt att borra monteringshål för skruvarna i flänsarna. I denna form är matrisen redo för borttagning.
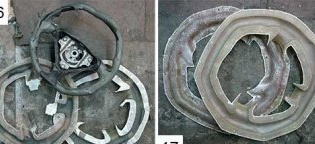
16.Med ett knivblad eller en tunn stållinjal kopplar vi bort flänsarna runt hela konturen. Sedan utvidgar vi mellanrummet mellan flänsarna och separerar matrisens halvformer. Ett tunt lager plastinmodell under avlägsnandet av matrisen förstörs, delvis kvar i halvformer.
17. Plasticinrester tas lätt bort från matrisen. Sedan kan den inre ytan torkas med fotogen. Jag rengör konturerna på flänsarna med sandpapper. På arbetsytan för den rengjorda matrisen är defekter i plasticinmodellen tydliga, vilket jag korrigerar med samma sandpapper.
Även med denna grova matris kan du göra flera dussin roder. Men vem kommer att ge dig så många identiska rattar för att ställa in? Men exklusivt arbete med plasticin och glasfiber är mycket efterfrågat.
Del två:
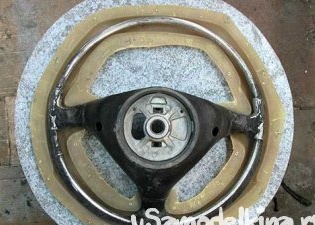
Den grova matrisen som framställts med användning av vanligt polyesterharts (till skillnad från det slutliga matrishartset) har betydande krympning och krympning, vilket leder till förvrängning av den ursprungliga formen. Dessutom, ju mindre och mer komplex del, desto mer synlig är deformationen. Särskilt starka uttag inträffar i hörnen, som i vårt fall längs hela formen av halvformen. Så vid deras fullständiga polymerisation samlas synliga missförhållanden i en halvform relativt en annan längs konturen i själva ratten. Men för det är det också en grov matris, bara för att hjälpa oss att överföra plasticine-idén till ett fiberglasämne i den framtida formen, eller tjäna som ett tillfälligt (billigt) verktyg för att studera efterfrågan på en ny produkt.
01. Innan du börjar göra halvor av ratten förbereder jag ratten för att klistra in. För att gradvis skära bort överskottet av gummi från fälgen och ekrarna satte jag ratten i matrishalvformen. Samtidigt försöker jag att lämna så lite utrymme som möjligt mellan fälgen och ytan på matrisen för limning.
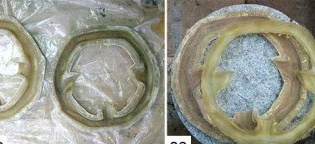
02. Du kan limma rattskorporna på en gång, omedelbart lägga två lager av 300 mm glasmatta. Det viktigaste är att försöka bilda ”torrt”, det vill säga ta bort överskott av harts med en pressad borste.
03. Ett föremål med en tjocklek på två lager tunnglasmatta visar sig vara sprött, så det måste tas bort från matrisen med försiktighet. Jag klickar på kanterna på glasfiber som sticker ut längs matrisens kanter mot varandra och drar försiktigt ut jordskorpan.
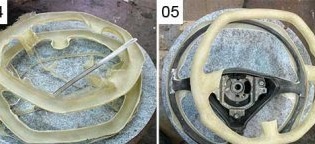
04. De ojämna kanterna på de borttagna delarna måste skäras i enlighet med utskriften som finns kvar på delen av matrisens kanter. För trimning kan du använda ett elverktyg eller såga med en bågsåg för metall.
05. Jag försöker på skorporna till ratten, medan jag trimmar, om nödvändigt, ratten gummi. För bättre passform av delar, bör den inre ytan på glasfiber rengöras med grovt sandpapper och ta bort stickande glasfibernålar och hartsflöden.
06. Gradvis modifiering av delarna och fälgens kanter passar jag halvorna på varandra på rattet. Väl kombinerade och fritt sittande på rattskorporna är klara för limning.
07. Det finns två sätt att limma halvformar. Vanligtvis förs de delar som ska limmas in i matrisen, som i monterat tillstånd kombinerar dem och pressar mot fälgen. Men jag bestämde mig för att montera ratten utan att använda en matris. Jag ville kontrollera noggrannheten i kombinationen av delar och kvaliteten på att fylla med självhäftande material i hela utrymmet inuti rattet och i sömmarna. Som limning använder jag en blandning av polyesterharts, aerosil (glaspulver) och glasfiber. Det visar sig att gröt liknar en glasfylld kitt, bara härdningstiden är mycket längre. Med denna komposition fyller jag ratthalvorna och pressar dem på fälgen. Jag tar bort överskottsgröt som pressats ut från sömmarna och fixerar halvformerna med maskeringstejp. Korrekt deformerade platser för skorpor korrigeras med klämmor.
08. Uppvärmning av en del indikerar en intensivt pågående polymerisationsreaktion. En och en halv till två timmar efter limningens början tar jag bort tejpen och tar bort det återstående hartset. Därefter kan rattens yta bearbetas.
09. På alla delar som tas bort från matrisen finns spår av separationsskiktet. Därför är det första jag rengör med sandpapper allt glasfiber från resterna av separatorn.
10.Traditionellt står en inställd ratt inför kolfiber (kolfiber), träfanér och äkta läder. Fasta material med en lackerad yta placeras på den övre och nedre delen av fälgen, och sidodelarna med rattens ekrar är täckta med läder. Så vi planerade först att göra på rattet. Men efter att ha hållit en nästan färdig bagel i våra händer blev det tydligt för oss att den extrema utformningen av formen krävde en ovanlig finish. Och det beslutades att göra allt tvärtom, det vill säga huden ovan och under, med faner på sidorna.
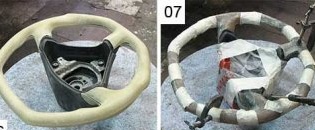
11. För större komfort kan ett tunt lager poröst gummi limmas under huden (vilket kraftigt ökar arbetskostnaderna). En ungefärlig bit av något större storlek än nödvändigt limmas på glasfiberrattkanten.
12. Gummi passar tätt i fälgen. På platser med läderinsatser limmas även gummipalmer enligt ett mönster under handflatorna. Alla fragment av gummi jämnas ut med sandpapper, och defekterna repareras med gummikrumm blandad med lim. Konturer beskärs enligt mönster.
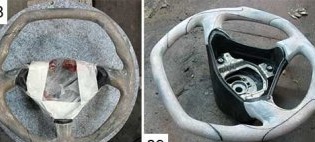
13. När vi planerar att avsluta ratten måste du ställa in rätt förhållande mellan fälgens storlek vid skarvarna i olika material. Så, till exempel, är tjockleken på faner med lack (upp till 2 mm) lika med tjockleken på huden med lim. Detta innebär att kanten på rattet ska ha samma tvärsnitt vid fogarna. Ett gummi limmat under huden bildade ett steg 2 mm högt på kanten. Därför måste du justera kanten vid fogarna med kitt. För att inte förstöra kanterna på gummimärkena med kitt måste de maskeras med maskeringstejp. För samma ändamål stickar jag en tunn plasticinremsa längs gummikonturen, som blir ett gap för att täta huden.
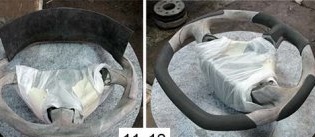
14. "Hårig" kitt är ett oumbärligt material i brödskivans arbete. Denna kitt är gjord på basis av polyesterharts och blandas väl med vårt polyesterfiberglas. Jag vet också att många hantverkare gör rattet helt och hållet av kitt. önskad form.
15. På rattens sista yta markerar jag sprickorna för att täta huden. Snitten på fälgen görs mest bekvämt med ett metallbågssågblad. Spaltens djup bör vara minst 3-4 mm och en bredd på upp till 2 mm. Jag klippte snitten med en trasa med sandpapper. Spår av insatser under handflatorna var markerade med plasticinband. Efter att plastin har tagits bort justeras spåren med kitt och sandpapper. Det är mycket bekvämt att lägga mellanrum "bormaskin".
16. Den sista handen är installationen och montering av krockkuddehöljet. Det viktigaste är att korrekt beräkna luckorna. Faktum är att det rörliga locket inte bör gnida mot ekrarna. Dessutom måste du lämna utrymme för hudens tjocklek eller Alcantara, som täcker airbag-locket.
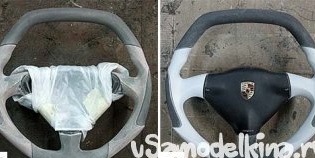
För passformens noggrannhet sätter jag in läderbitarna i springan och "pumpar" rätt plats. För att passa in i luckorna används alla samma medel - kitt och sandpapper. Jag avslutar glasfibern med en grunder så att hela formen visas, eftersom det är svårt att se den prickiga ytan från kittet defekter.
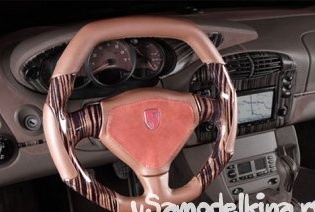
Detta slutar arbetet med prototypen och produkten skickas till andra specialister. Först kommer en mästare att klistra in fanér och lackera den, sedan kommer en annan mästare att täcka den med läder. Det slutliga resultatet kommer att bero på efterbehandlarnas kvalifikationer, men layoutmästaren med dess ergonomi, plasticitet och proportioner ger layouten. Därför har den grundläggande specialiseringen i tillverkning av icke-standardprodukter alltid varit produktion av brödskivor.